News & Events
Catch up on the exciting news and events at Silverstone Park.
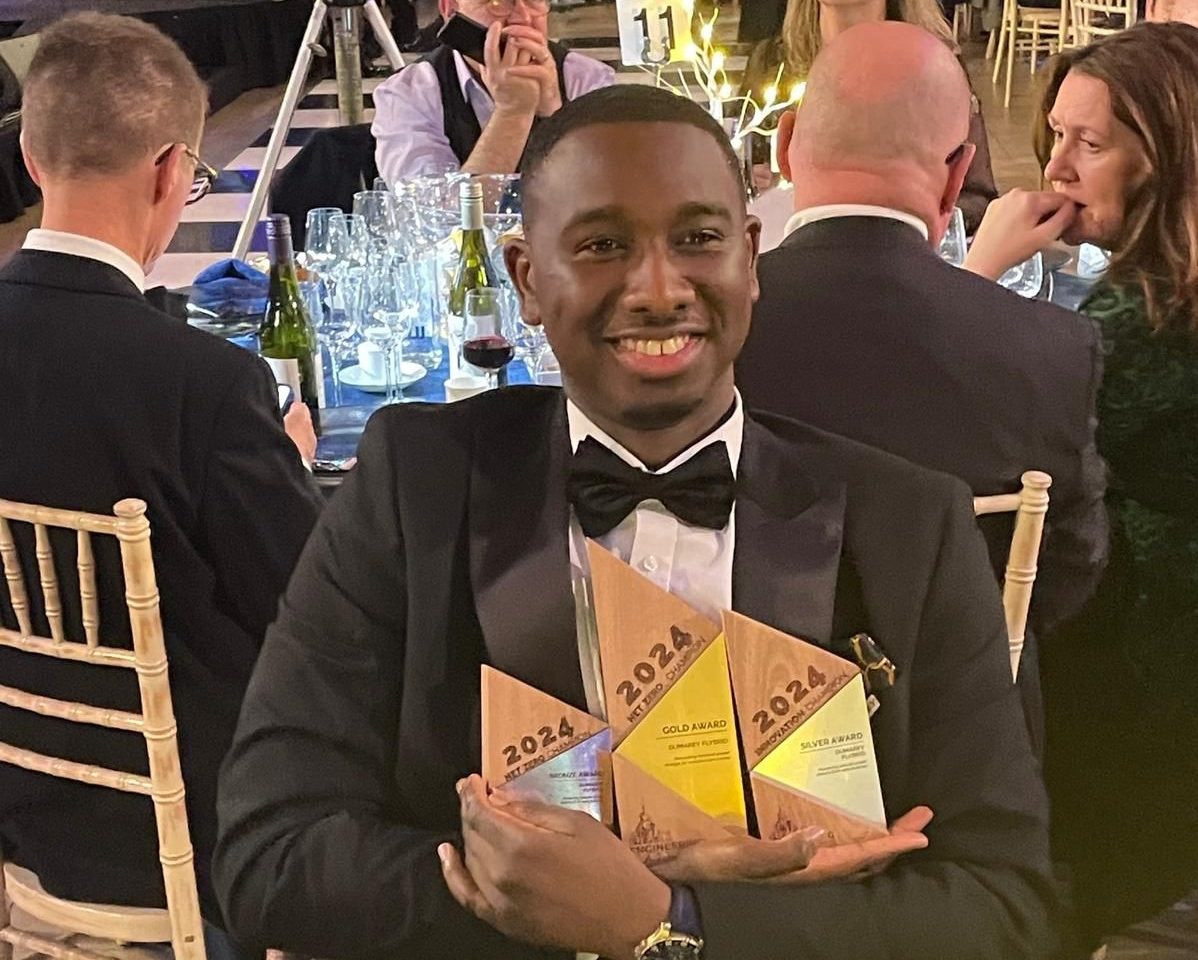
18 Apr 2024
Hat-trick for Dumarey Flybrid at Engineering Matters Awards
Silverstone Park business occupier Dumarey Flybrid’s innovative work in clean energy technology has been further recognised with three high-profile industry awards.